
- This event has passed.
Dissertation Defence: Data-Efficient and Uncertainty-Aware Hybrid Machine Learning in Advanced Composites Manufacturing
April 27, 2023 at 8:30 am - 12:30 pm
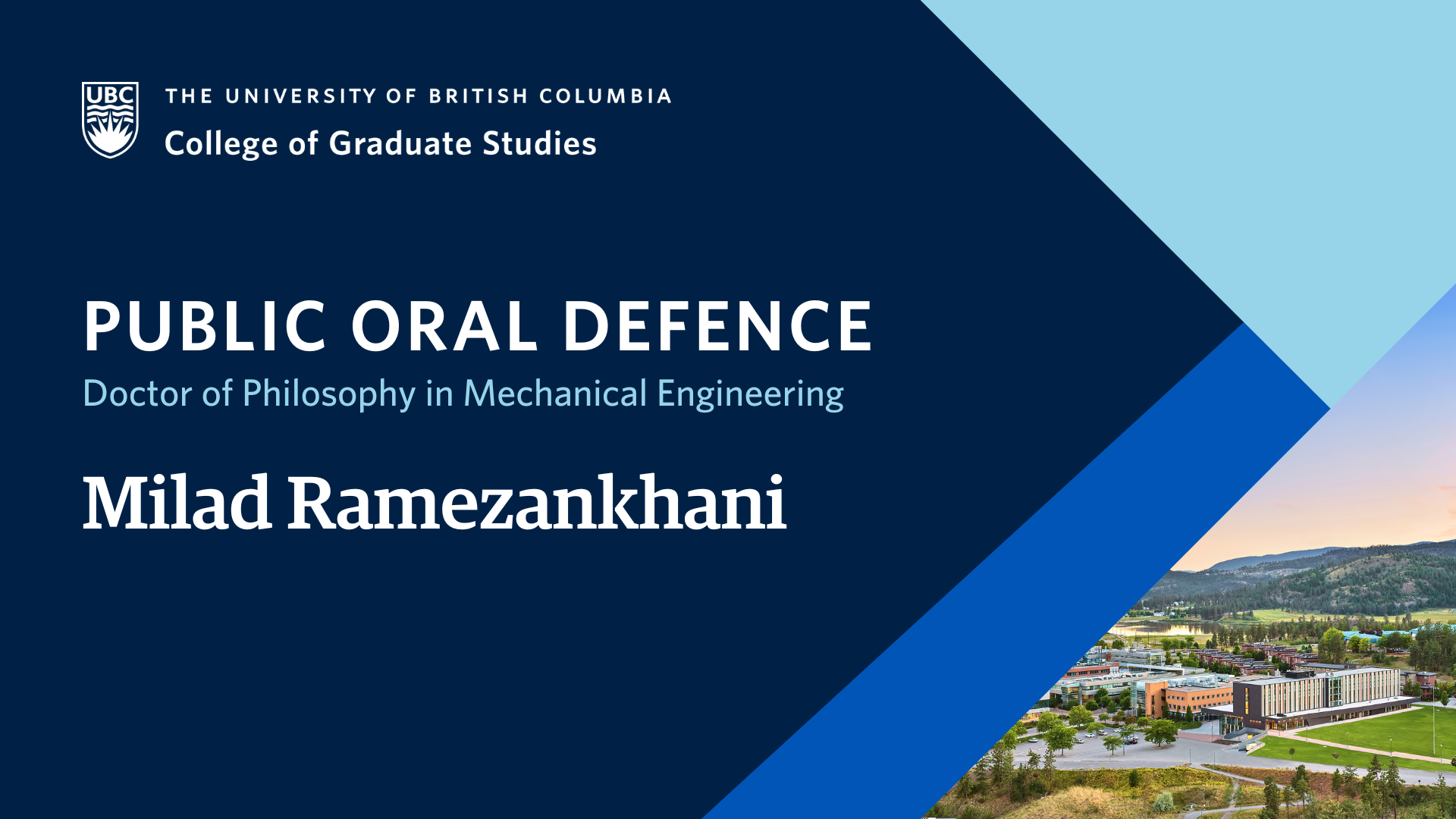
Milad Ramezankhani, supervised by Dr. Abbas S. Milani and Dr. Rudolf Seethaler, will defend their dissertation titled “Data-Efficient and Uncertainty-Aware Hybrid Machine Learning in Advanced Composites Manufacturing” in partial fulfillment of the requirements for the degree of Doctor of Philosophy in Mechanical Engineering.
An abstract for Milad’s dissertation is included below.
Examinations are open to all members of the campus community as well as the general public. Registration is not required.
ABSTRACT
Machine Learning (ML) has evidently become one of the cornerstones of Industry 4.0, an emerging vision toward transforming manufacturing enterprises into smarter and more customizable units. Among different ML techniques, deep learning has shown ground-breaking potential for advanced manufacturing applications under complex and highly nonlinear processes. Despite its unparallel advantages, some limiting factors currently prevent the exhaustive cultivation of deep learning by industries. Namely, in many practical scenarios, deep learning’s big data prerequisite is prohibitive as temporal and financial costs of data collection are often notoriously high. Besides, for high-risk decision-making settings such as aerospace-grade composites manufacturing, the problem of learning the system’s behaviour under limited data is exacerbated by the inevitable materials/process uncertainties. To address these gaps, this thesis aims to develop a series of data-efficient and uncertainty-aware hybrid learning models for advanced composites manufacturing, as part of a holistic AI-assisted decision-making tool towards Industry 4.0 applications. First, transfer learning and its hybrid with active learning are used as a base strategy to assess knowledge transferability across different composites manufacturing processes. It is shown that auxiliary information, such as abundant data from related low-cost processes, can be used for efficiently learning the costly process of interest under data scarcity. Next, a sim-to-real transfer learning framework is developed to tackle high-dimensional, heterogeneous and limited data distribution problems using numerical simulations. It is demonstrated that transferring knowledge from inexpensive heat transfer simulations improves the performance of deep learning in processing limited and high-dimensional thermal images collected at a factory. Next, a multi-fidelity learning framework is proposed as another gateway to leverage the abundant low-fidelity information and learn high-fidelity systems. Namely, by incorporating the established physical laws in the composites field, the ensuing multi-fidelity physics-informed neural network model shows to be successful in further reducing the dependency on acquiring costly experimental data. Finally, a novel hybrid Bayesian framework is proposed to quantify aleatoric and epistemic uncertainties in the training of data-efficient models developed in the previous case studies. The quantified uncertainties, while enhancing the ML performance in highly noisy regimes, would serve as a vital means for decision-makers in Composites 4.0 practices.