
- This event has passed.
Thesis Defence: Additive printing of porous geopolymer concrete: assessing design mix and printability
May 16, 2024 at 1:00 pm - 5:00 pm
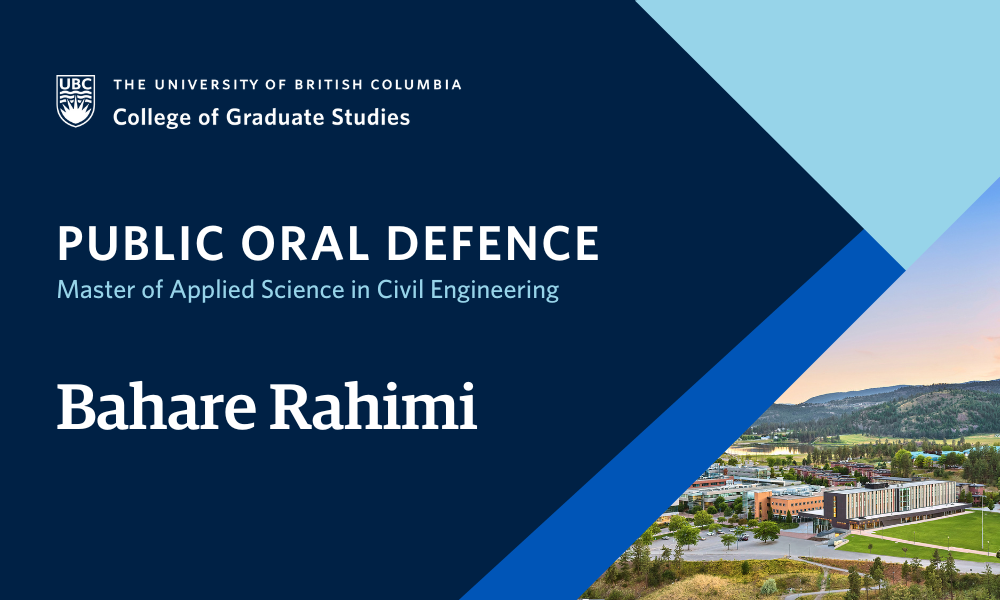
Bahare Rahimi, supervised by Dr. Sumi Siddiqua, will defend their thesis titled “Additive printing of porous geopolymer concrete: assessing design mix and printability” in partial fulfillment of the requirements for the degree of Master of Applied Science in Civil Engineering.
An abstract for Bahare Rahimi thesis is included below.
Defences are open to all members of the campus community as well as the general public. Please contact sumi.siddiqua@ubc.ca to request a Zoom link for the defence.
ABSTRACT
This research delves into the 3D printing of a previously developed porous geopolymer, a material synthesized from an alumino-silicate source through polycondensation initiated by an alkaline activator. The binder used in this formulation was a combination of fly ash (FA) and ground granulated blast furnace slag (GGBFS), while the alkaline activator (AA) was a mixture of sodium hydroxide (NaOH) and sodium silicate (Na2SiO3). To create porosity, 30% hydrogen peroxide (H2O2) was employed as the air-incorporating agent. The printer was an extrusion-based 3D printer chosen for its significance to the construction industry.
The complexity of 3D printing arises from the interplay between printer settings and the mix’s properties in different stages including mixing, pumping, extrusion, and the building stage.
In this study, the printer settings were kept constant to eliminate the printer’s influence on the outcomes, allowing any improvements in print quality to be attributed solely to modifications made to the mix formula.
Throughout the printing process, several stages presented challenges that led to the introducing of different additives: siliceous sand (SS), polyethylene glycol (PEG), and urea. These were chosen to mitigate uncontrollable flow, inability for structural recovery post-extrusion, and constrained working time. To understand the impact of these additives, rheological assessments were performed, including flow curve tests, strain sweep tests, and modulus recovery tests, aimed at evaluating the mix’s apparent viscosity, yield stress, and structural recovery capabilities.
The results highlighted the essential role of polyethylene glycol (PEG) in this particular geopolymer formulation, which is required due to the mixture’s inherent challenge in recovering its structure post-extrusion. The addition of siliceous sand notably improved the geopolymer’s overall printability. Conversely, urea did not prove effective in extending the working time.