
- This event has passed.
Thesis Defence: Performance and Repair Applications of 18Ni-300 Maraging Steel Printed with Micro-spot Laser Directed Energy Deposition
August 1, 2024 at 9:00 am - 1:00 pm
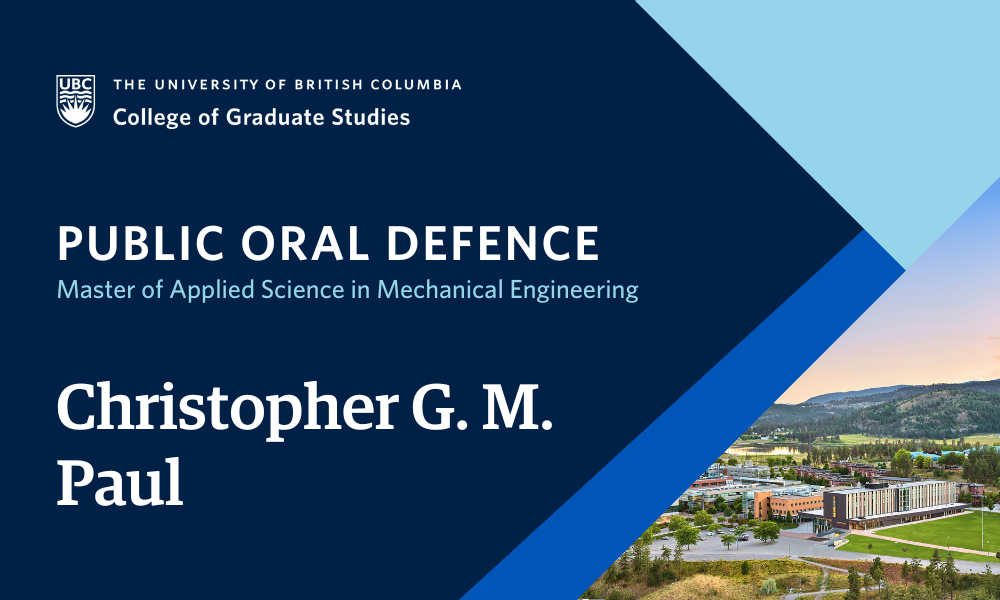
Christopher G. M. Paul, supervised by Dr. Michael Benoit and Dr. Lisa Tobber, will defend their thesis titled “Performance and Repair Applications of 18Ni-300 Maraging Steel Printed with Micro-spot Laser Directed Energy Deposition” in partial fulfillment of the requirements for the degree of Master of Applied Science in Mechanical Engineering.
An abstract for Christopher G. M. Paul’s thesis is included below.
Defences are open to all members of the campus community as well as the general public. Registration is not required for in person defences.
ABSTRACT
Additive manufacturing (AM) technologies are invaluable for the manufacturing industry by enabling repair of high-value components. Utilizing AM technology such as laser directed energy deposition (L-DED) to repair casting inserts by can increase tool life, reduce metal waste, and lower operating costs. Typically, L-DED systems employ a 1–3 mm diameter laser spot to melt feedstock material. However, recently developed novel micro-spot L-DED systems, if optimized correctly, can enhance repair applications by creating smaller beads and further minimizing heat input. This thesis aims to optimize parameters for a micro-spot L-DED system and apply these parameters to a proof-of-concept repair process for a high-pressure die casting (HPDC) insert.
By varying main L-DED printing parameters, the deposition behavior and optimal settings for achieving high-density maraging steel were determined using a micro-spot L-DED system. Single-track experiments defined a processing window for ideal bead shape. Volumetric samples were then printed, and optimal process parameters which created high-density material (>99%) were selected. Compared to larger laser diameters, the 0.3 mm laser significantly influences bead formation characteristics, weld pool stability, part shape accuracy, and internal defects. Internal defects such as pores and titanium oxide inclusions reduce tensile strength and ductility, though these values remain reasonable for this material. Additionally, variations in grain structures found throughout the deposited material were correlated with changes in cooling rate during L-DED.
The developed L-DED repair process for the damaged HPDC insert removes the heat check crack and deposits material with micro-spot L-DED, restoring the component’s geometry. The repair process, along with subsequent external (geometric accuracy) and internal (microstructure and microhardness) analyses, provides valuable insights into the microstructural and microhardness differences between the softer deposited material, the harder base material, and the heat-affected zone.
This work showed that micro-spot L-DED is feasible for repair, but it also showed key areas in the repair methodology that require improvement before industrial implementation. Additionally, the response of maraging steel beads and cubes to L-DED parameters warrants further investigation, focusing on optimization of gas flow and powder feed rate settings with lower heat input, to address printing behavior unique to micro-spot L-DED systems.